
Report by Paula Antolini, October 17, 2019, 7:45AM EDT

Are you aware that your life and the lives of your family and pets has possibly been at risk for years because you are not protected by the Town of Bethel in the manner that you assumed, in the event you are in a fire or other emergency?
Presently the Bethel Fire & EMS fire department is urging the Board of Selectmen (BOS) to remedy this situation of an improperly working extremely aged aerial tower truck that the FD has been struggling with for years, but they are hitting roadblocks from the BOS that are unnecessarily complicating and delaying the process further. It also appears that even if a solution is approved by the BOS it would still be a year before a replacement is in place. So this means residents may remain at risk even longer. Having to depend on mutual aid for a ladder truck to arrive from another town could add a precious ten minutes of delay to a call, Chief Engineer Bill Cadella said.
Some members of the Bethel Fire & EMS fire department attended the Board of Selectmen regular meeting on October 15, 2019, to discuss replacing the aerial ladder truck, particularly the extension ladder, which is presently not working and has not been properly operational in several years. It is 42 years old, resting on a chassis that is 11 years old, and both continue to have numerous repair problems.
On observance of the October 15th BOS meeting, it appears that the fire department officials did their due diligence in thoroughly researching facts and supplying the Bethel Board of Selectmen with much information regarding replacement costs or refurbishing/repair costs, but the BOS is still delaying the process more and asking for second opinions and more research on repair companies and other things, despite the extensive information (verbal and written) provided at the latest BOS meeting and the dire situation.
This means not only have Bethel residents’ lives been at risk for years but now there seems to be no urgency to fix broken fire department equipment and the FD is operating at a detriment, not only to residents, but also to volunteer workers of the fire department. This is because it could still take a year even with approval, to obtain new equipment. Also, inferior equipment could be catastrophic if a incident occurred where an extension ladder was needed and no mutual aid was available or could not get to the site because of low bridges, which is another concern.
Improperly working equipment could also malfunction while volunteer fire fighters are on their way to a scene, thus causing unnecessary injury or death to them or others in a traffic accident, or in related accidents at the scene if, for example, ladders do not work properly or a truck is not stabilized according to present standards, to stop it from toppling over, or to stop a ladder from crushing the truck cab or the side of the truck if not working properly when extended in that direction. “The truck never got any of those updates,” said Chief Engineer Bill Cadella.
Cadella referred to the National Fire Protection Association (NFPA) standards that are supposed to be adhered to, to which some of the current equipment does not confirm. Cadella said anything that is not compliant has to get updated, items on the vehicle such as “computers, the entire electrical system has to have the new multiplex system to operate everything electronic, the vehicle’s onboard computer, that’s the brain of the truck, this truck doesn’t have the newest version of that so that has to get updated, anything power-train related that’s not compliant to current standards has to get updated, so by the time you’re done with that project you’ve basically replaced everything but the walls of your cab and the frame rails and your motor.” Cadella said the last time they looked into that it was $750,000 from Sutphen, and would take a year to do the project and that, “They (Sutphen) really did not want to take on that project.”
Selectman Straiton asked Cadella, “In the past 42 years since you’ve had that truck you never crashed or tipped it over?” Cadella replied, “There’s some damage on the roof where it’s tapped a couple of times. Thankfully we never had a significant incident where it was in danger of tipping over. it has struck the cab a couple of times.”
Selectman Paul Szatkowski stated, “I don’t know about you but I’d like to get a third party, because I’ve gone on the internet when I first heard about this. There are places, I’m sure you know about them too, Pennsylvania, Ohio, and even out west, they’ll totally retrofit. They say, “We can do anything relative to hydraulics and ladders.’ The question is, how much is it going to cost.”
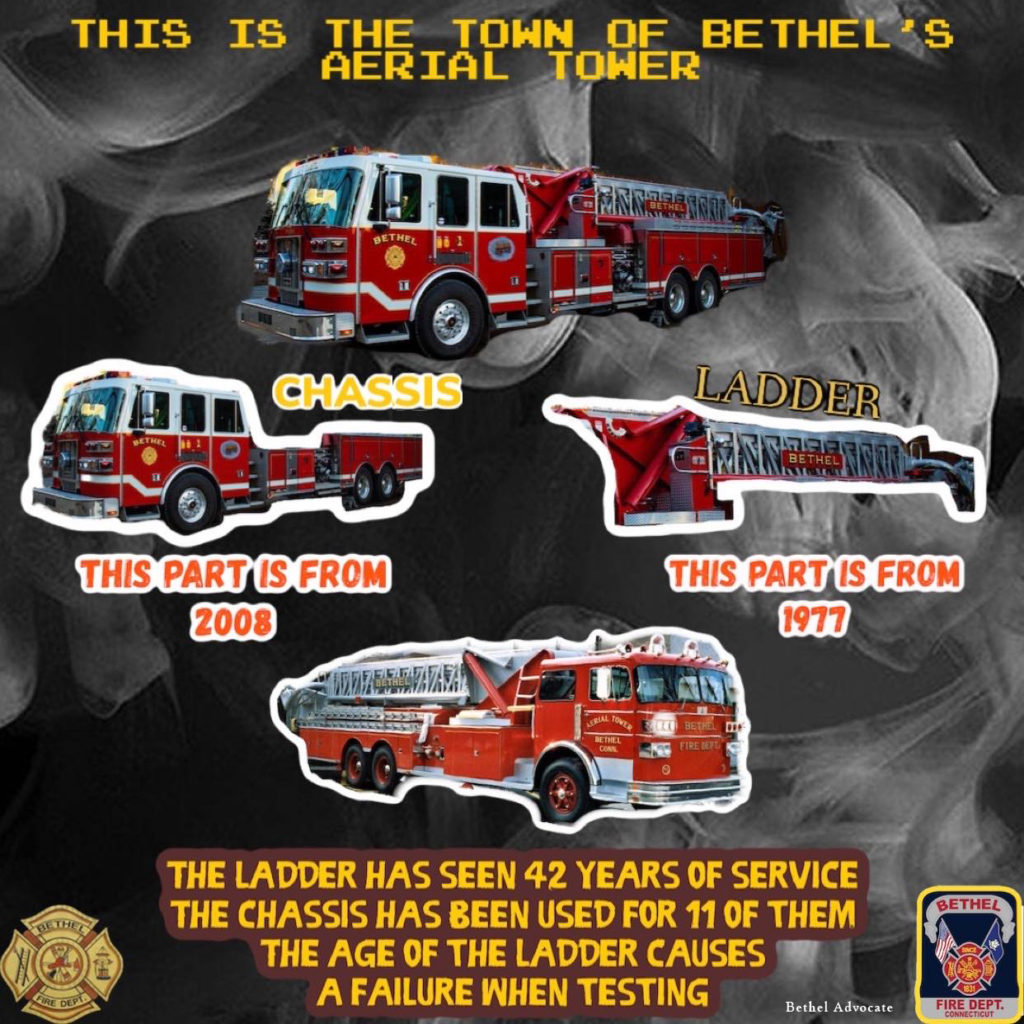
BOS October 15th Agenda item: CONSIDERATION OF A FIRE TRUCK
The South Street Bethel Fire & EMS fire department is asking the Board of Selectmen to approve replacement of their fire truck ladder, that has a reach of 90 feet, and is 42 years old, and possible the chassis too, that is 11 years old, due to it’s present non-working condition, and extensive repairs constantly needed, especially over the last 14 months. New equipment is also needed due to the fact that the equipment is outdated because standards have drastically changed over the years and presently the equipment does not pass inspection, said Chief Engineer Bill Cadella.
The chassis pretty much needs to be “stripped down to a shell on the inside” to adhere to present standards, said Cadella, and the ladder replaced, both at a cost of approximately $1,400,000 to $1,600,000 for a new truck and ladder vs. $750,000 (in 2018) to repair or refurbish everything. These repairs were NOT recommended to do, by Tom Sutphen of the Sutphen Corporation, basically because of the same issues the FD was running into, Cadella said, with “matching old and new equipment parts.” If Sutphen did choose to do it, Cadella said Sutphen said they would have to make the rest of the truck compliant to the new standards as well.
However, if the BOS chooses to refurbish rather than replace the the old equipment, the problem is getting parts for old equipment and finding someone willing to refurbish the equipment at a reasonable charge, Cadella said, and then there are no guarantees on equipment.
Straiton also asked the FD to find out about “leasing” and “payment plans” and said they needed to do their “homework.” Straiton did comment that he “could not see putting $750,000 into the equipment” if they then “had to refurbish the entire rest of the truck” too.
Even though the last BOS meeting scheduled for October 1st was suddenly cancelled with no reason given, and now on October 15th, 2 weeks later, Knickerbocker indicated that the fire department gave the Board of Selectmen (BOS) some “test reports” and said, “To be honest, I have not had time to look through this.” He said basically he wanted the BOS to have an opportunity to “ask them questions for specs they needed, the time lines, what the longer range plans are.”
Knickerbocker began by referring to the current chassis as 11 years old and asked, “What kind of shape is that in?
Cadella replied it was in “good condition” and they “maintained it” but that in the past 14 months they had “transmission problems and motor problems that had to be addressed” and said, “Its something to be expected with a truck of that age but it’s at that age where it’s experiencing more and more of those wear and tear issues.” Cadella said, “There was an issue with the electronic transmission not shifting properly, the computer had to get replaced. There was an issue with the interface between the transmission and the motor for the Jake brake that required more electrical repairs. The air brake system, the air dryer has been replaced three times. The compressor has been replaced once, the air governor has been replaced twice, and I’ve had, so far, two of my ABS sensors have gone bad. We had to replace all of them because all of them were the same age, they were all subject to the same problem. That’s the past 14 months with that power train.”
As Chief Engineer Bill Cadella made a lengthy presentation detailing the numerous issues with the equipment, and detailing the problems with refurbishing the ladder and truck, the issue mainly concerned the high cost of replacement labor and parts, IF they can even find parts, and the fact that they are then left with equipment that has no manufacturer guarantees after it is patched together, IF you can find someone to do the restoration. A trip to Pennsylvania was mentioned, for one repair operation, in which they would also be charged for gasoline on the return trip. He said they are having a hard time locating people willing to do the work locally or at all.
All three selectmen questioned the firefighters extensively, asking them to get a second opinion, or a more detailed “specs” report, or even consider other manufacturers, even after Chief Engineer Cadella said they did extensive research. So basically the BOS requests are now delaying the replacement process even further, which could take as much as a year to order and manufacture a replacement, even if it is approved, Cadella said, possibly leaving Bethel residents at risk should a catastrophic fire occur and they cannot obtain mutual aid. At the present moment Cadella said they can drive the aerial ladder truck to an incident, because they need the equipment on the truck, but park it to the side in order to allow mutual aid to bring their ladder truck to the scene to help.
Selectman Paul Szatkowski asked Cadella what the exact problems were with the ladder. Cadella replied, “What caused it to fail inspection this year, because it failed two years in a row, what caused it to fail this year is the hydraulic valve body, which is the part of the hydraulic system that operates the aerial device, it’s bypassing fluid so when the controls to lift and lower the ladder and extend and retract the ladder, when you let go of them they are supposed to return to the neutral position and stop the movement of the ladder. They’re not doing that.”
Cadella continued, “So along with that there is a violent vibration that developed in the turntable to the device. The aerial boom mounts to a turntable so it allows the boom to spin 360 degrees, and the table mounts to the chassis. So this vibration is starting to cause wear on the hydraulic swivel within the turntable mount.” Cadella said that model of the swivel and the valve body itself has not been made since the mid-90’s. “At that point when the manufacturer was updating their designs thats when they stopped making it,” Cadella said, “They haven’t been able to get those parts. They tried a solution of trying to piece together parts of a new valve body with old components and vice-versa to make it work, last year, when we failed last year. They were unsuccessful at doing that. The best combination of parts they could cone up with, it still has the final vibration. They told us, after giving us the truck back after having it for six weeks, ‘This is as good as it’s going to be, we don’t know what’s wrong with it, we can’t figure out why.’ ”
“This was Sutphen?” asked Knickerbocker. Cadella said, “Yes.”
Knickerbocker asked Cadella, “Are any independent repair places that specialize in this kind of apparatus to could get another opinion?” Cadella replied that there is one in Connecticut called ‘Five Star’ in East Hartford, who he said was the territorial Sutphen service center for this part of CT and a couple of the surrounding states. “They are part of the Sutphen franchise. They were our primary service center as anything Suphren related gets diverted to them. But because of the poor service we’ve been receiving there both with this truck and Engine 5 which we to delivery of about 5 years ago, we had to go through a whole proceedings with the Sutphen Corporation to get ourself legally removed from our obligation with Five Star.” … “They were not performing, the quality of their work and the time that it took to do it were creating problems for us.” … “They are the authorized dealer and service center in CT.”
“When we contacted Sutphen Corporate and said, ‘This isn’t working. We need a better solution,’ they made up a contract, if you will, saying that we can deal directly with the Sutphen East plant, which is out in Pennsylvania,” Cadella said. This would require the truck to get driven 3 hours to Pennsylvania and 3 hours back, so they “lose a whole day” Cadella said, and then the FD is billed for the fuel on the way back. He said they incurred the same problems with the company fixing or addressing repairs in a timely manner, or not returning phone calls or emails and the truck was there for 6 weeks. It took a month before they replied to messages about the status of the truck, Cadella said, “I don’t want it done fast I want it done right, but logistically I need a idea of how long the repairs are going to take. Are we talking a week or 2 months, I just need to know so we can plan for our operations.” The company replied, “We really have not performed this type of repair so we really don’t know.”
Cadella said they switched manufacturers because of all these problems and are buying the Seagrave brand now, whose repair center is right in Brewster, NY. “Its been a day and night difference with the service we received, both from Hudsion Valley Fire and the Seagrave Factory,” Cadella said.
Selectman Richard Straiton asked, “So there’s no other independent contractor or service people that can work on that hydraulic system?”
“Our options right now are the manufacturer at their satellite facility in Pennsylvania, or going back to Five Star,” replied Cadella. He said even if he could find a repairman to work on the equipment the parts are just not available and even the manufacturer said the parts have not been made since the mid-90’s.
Chief Scott Murphy said, “A lot of the issue with that truck. That was the first time a refurb was tried with a Sutphen. Tom Sutphen did it himself out in what was called ‘Tom’s Toy Box’ Ohio. Nothing was ever written down, that truck, when Tom Sutphen passed away, the truck passed away with him because everything was in his head on how that truck was built. He never wrote anything down.”
The Sutphen company eventually found that there were, “No schematics for vehicles, no mapping of hydraulic lines, no list of parts and components. It was one of the first ones ever done so there was no record keeping,” Cadella said, “There’s nothing for anybody to try and research to find out about it.” He said they have an owner’s manual to the power train and cabin chassis when that was manufactured as a new piece of equipment, but for all the new parts added there is nothing in print or on a computer to reference. The only manual Cadella said the FD has for the 42-year-old ladder is a “15-page typewriter document from the late 70’s when that was originally built.” Chief Murphy said theres no paperwork on connecting the two pieces.
The problems incurred at the recent Clark Business Park fire come to mind, which not only required numerous mutual aid to haul in water, but the additional issue of a local overpass to a bridge, being too low for equipment to pass under, which also pertains to the size/height of the aerial ladder truck or getting mutual aid to a scene in time. At the present time some trucks cannot pass underneath, leaving Bethel residents and businesses at risk.
Standards of what is required on equipment have also drastically changed in 42 years. Cadella said that trucks nowadays require stabilizers for example, so the truck does not topple over, or so the ladder does not crush the cab section of the ladder is extended over that part. Even the truck interior would not pass inspection now, Cadella said, due to seats needing to be larger to accommodate larger equipment the firefighters carry on their backs for instance, basically meaning the entire interior of the truck would need to be reconfigured to pass code.
Selectman Szatkowski talked about finding used equipment or parts and Selectman Straiton asked if the FD could find a “demo” available and to look at other brands of trucks.
First Selectman Knickerbocker said he would need to “put this out to bid” (even though on numerous occasions the Board of Selectmen has waived the bidding process when they feel it is necessary, for other projects).
“I think you guys have your homework,” said Knickerbocker, “I doubt that you’re going to want to keep the old one [truck] for a back up, we would need a quote on refurbishing that. We need you to submit the full technical specs … we may need to go through a bid process but we would also need the HG group or any other coop, cooperative arrangements, full technical specs, even of we needed to bid it out, I mean we really do have to show the taxpayers that we are doing our due diligence. And then the leasing or any other type of payment plans … and last but not least, keep trolling and looking for demos.”
“The problem we have is that, you know, we knew this truck needed to be replaced, we didn’t deal with it during the budget, I mean personally, I thought we still had some time to deal with that because these things come up kind of on a long range thing. This thing has gotten bad in a hurry and left you guys in a lurch.”
—First Selectman Matthew Knickerbocker
Knickerbocker said, “The problem we have is that, you know, we knew this truck needed to be replaced, we didn’t deal with it during the budget, I mean personally, I thought we still had some time to deal with that because these things come up kind of on a long range thing. This thing has gotten bad in a hurry and left you guys in a lurch. The lead time, like if we had a referendum next week and approved this truck, it’s going to take close to a year before we see it, and you’re going to need something. So, I mean, I’m hoping that we get lucky and somebody ordered what you need and they say, ‘Oh, our agency went out of business, we don’t want this anymore.” … “We can move this along fast if an opportunity comes up. Even if you had an opportunity, it is bound to be over a million dollars and we’d have to go through the bid to, maybe we can have an emergency town meeting to approve a deposit or something that’s below that, while we go through the process.” … “Our goal is to get you guys back in business and not have to be sitting there tinkering with a truck that doesn’t work, for a whole year, because that’s what we’re looking at.“
*****
BOS October 15th Agenda item: CONSIDERATION OF PARLOA PLAYGROUND EQUIPMENT
During another part of the same BOS meeting, Parks and Recreation Director Eileen Earle was requesting playground equipment for Parloa playground in Bethel, which was unanimously approved by the BOS at this meeting, for $35,945.66 as presented.
Knickerbocker responded, “This was anticipated in the Annual Capital Budget,” said Knickerbocker, “In the budget process it was removed from the Capital list and put into the Operating Budget, of Capital Non-Recurring, there is a line for it. We don’t have to go through a town meeting but we have to go to the Board of Finance for it to release those funds.”
Knickerbocker said, “I was not going to do this because it can’t start until the Spring, however, if we move this along now there is a grant available that offsets the cost by a little over $14,000″ and asked Park and Recreation to give an “explanation of the equipment” she wants to buy and “how the grant works.”
Earle said the grant was through Gametime Equipment ,“Which is a percentage off based on how much you purchase,” Earle said. (For a limited time, GameTime is offering up to 100% matching funds on eligible play systems. Grant funds are awarded based on need and on a first-come, first-served basis.)
Earle said they want to replace both playground equipment pieces because with the savings they can do both, and they feel both pieces need to be replaced, they are 25 years old.” Earle said the discount was about 30%, when asked by Selectman Paul Szatkowski. He replied, “Not bad … an oppportunity of a grant like that, why not.”
Earle said this is part of the “Master Plan” that the Planning & Zoning Commission approved last September, of which she provided copies to the BOS so they “could approve it at their next meeting,” she said. The budget was $32,000 at the time and now she indicated $35,000.
Knickerbocker said, “It’s basically a sales incentive, but we’ll take it.”
They will use the same company as they did with Meckauer Park, Earle said, and the desired equipment is “made of metal piping and plastic similar to what’s there” Earle said. The new plan includes a wood chips surface as before, and a rock climbing wall and a number of slides and contains new features in the toddler area, age group 2-5 and also the 5-12 age group area. Earle said they eliminated any “tubes for people to hide in” so the parents would have more visibility to watch their children. “That’s been a safety issue and we’ve had some [people] vandalize them,” she said. The equipment would be installed by her Bethel “staff and a local contractor,” Earle said.
Knickerbocker made a motion, “To approve the Gametime proposal to replace playground equipment at Parloa Park, in an amount not to exceed $35,945.66 and forward to the Board of Finance for their review and approval.” It was approved unanimously by the BOS.
Knickerbocker asked if they had to place the order by the end of October and Earle said they just have to have a signed contract.
*****
VIEW MORE PHOTOS OF THE MEETING BELOW:
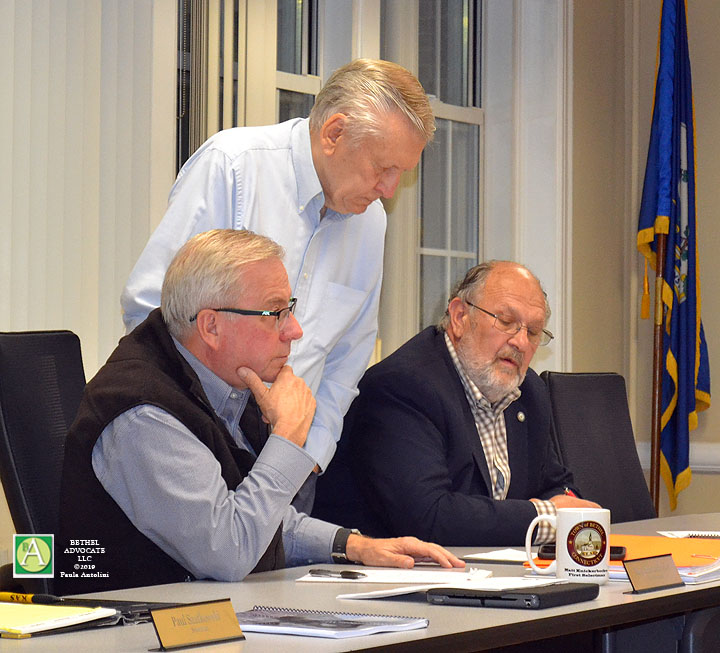
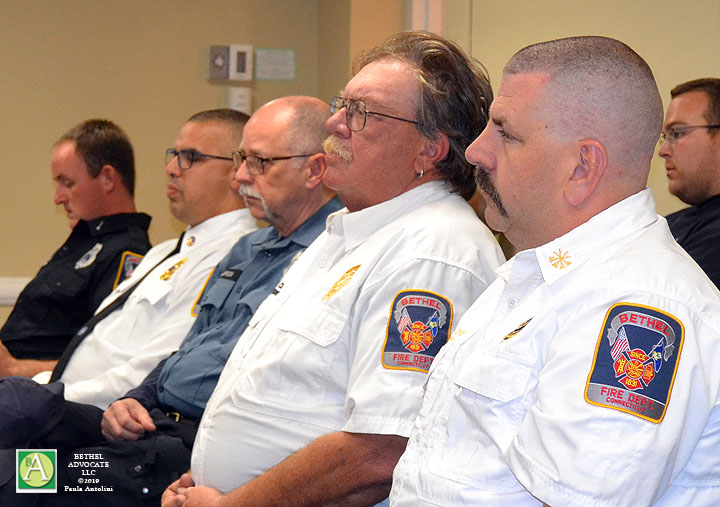
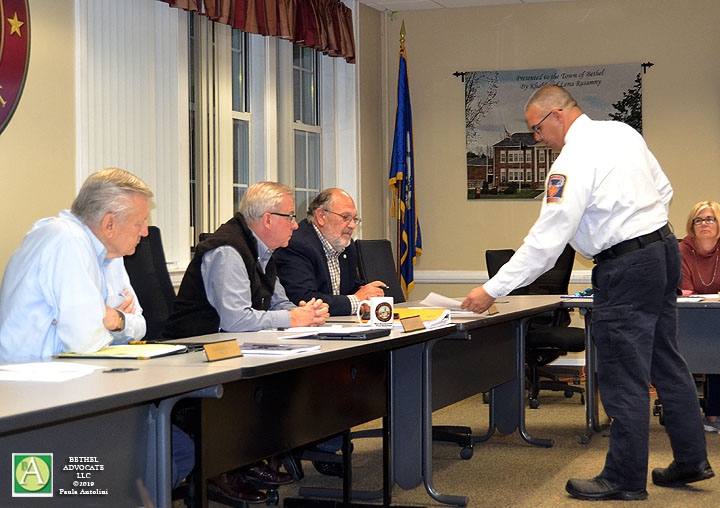
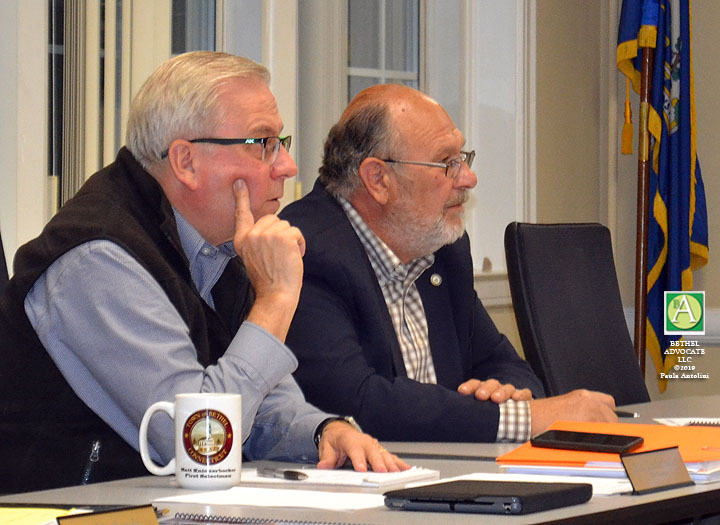
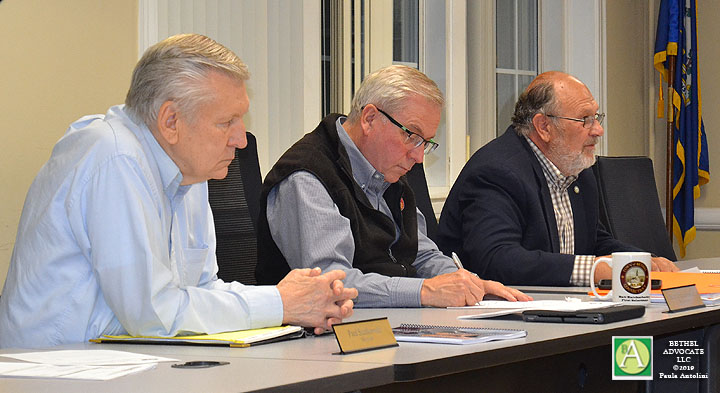
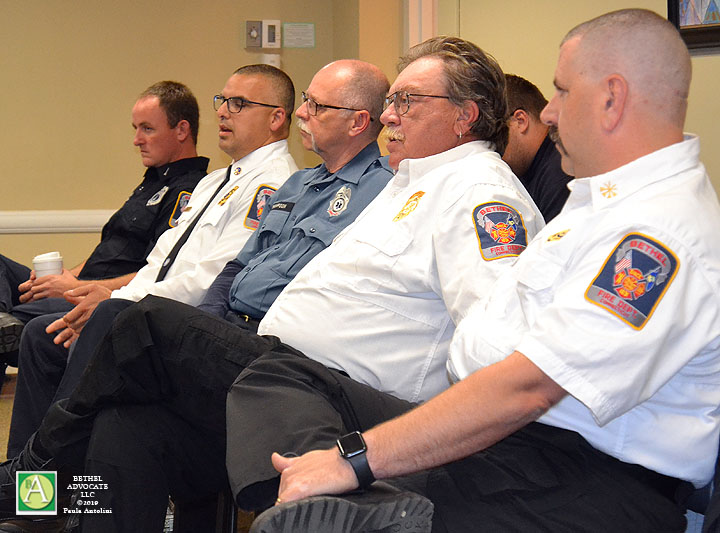
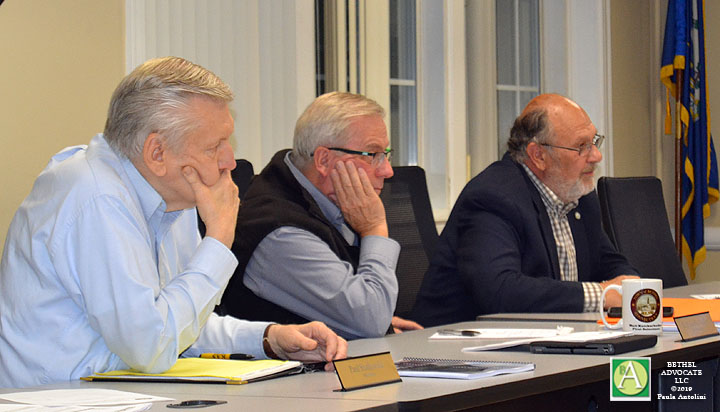
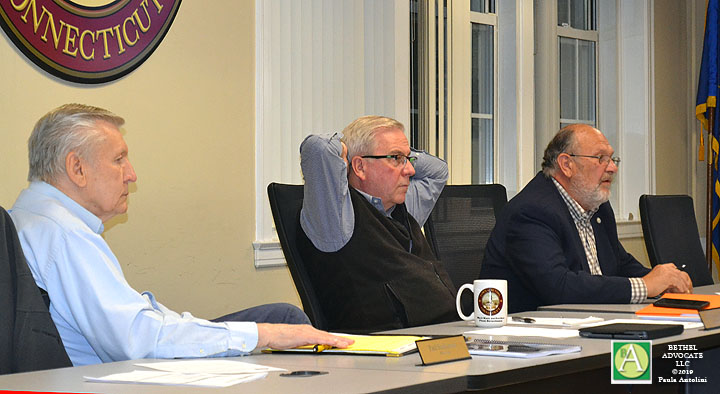
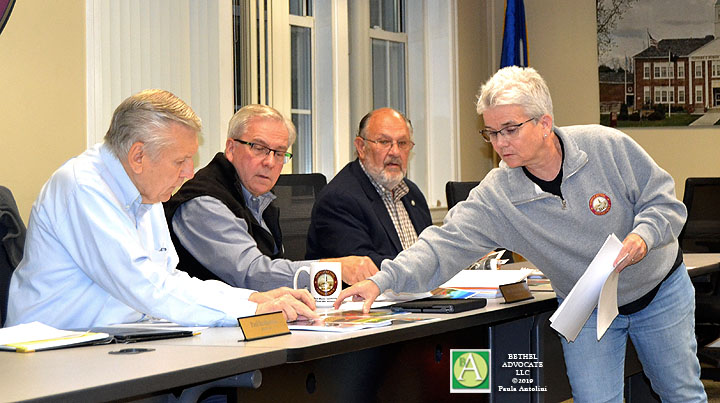
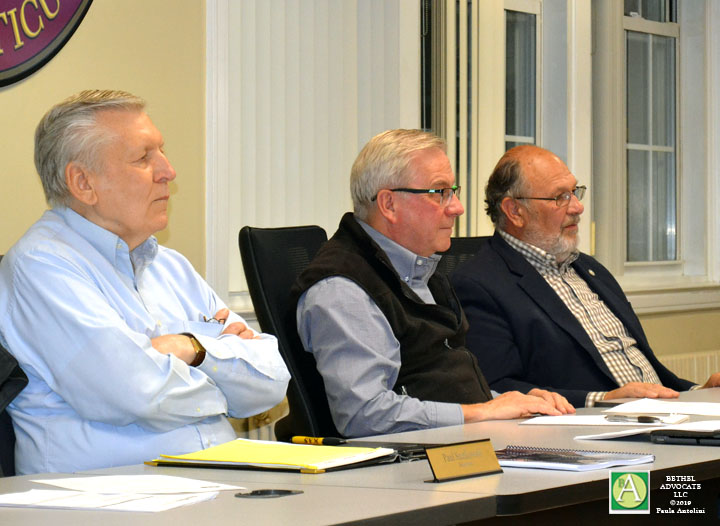
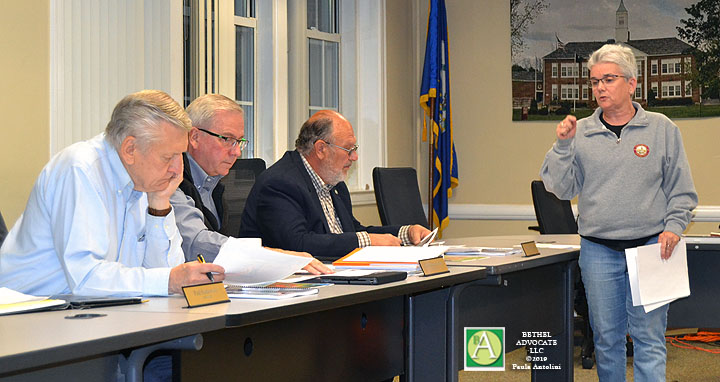
Video of meeting coming shortly, check back.
###
http://rxbuyonlinewithoutprescriptionrx.net/buspar.html
buy Lexapro online
Nexium no prescription
http://buywithoutprescriptiononlinerx.com/abilify.html